|
ICF vs Solid poured Concrete walls
Last Post 13 Nov 2014 07:00 AM by jdebree. 127 Replies.
|
Sort:
|
|
Prev Next |
You are not authorized to post a reply. |
|
Author |
Messages |
 |
|
BrianBaron
 New Member
 Posts:76
 |
29 Jan 2013 01:50 PM |
|
You're right Todd, we should go out and spend tens of thousands of dollars to have a thermal mass test done that less than 1% will understand or care about. Great idea. We have testing data that shows the exact R-Value calculations of our variety of R-Values. It looks very similar to the one posted above. If you are still referring to old statement that was made about the "Effective R-Value of 50+" from the R-22 form... I agree that was a bit of BS, but had some valid points to in pertaining to the air tightness etc. Thankfully the ICFA put somewhat of an end to it. I was looking at one of my competitors website the other day and they still have that on their site. Don't fault salesman for being salesman, the majority of the country is a salesman in one form or another. An engineer sells his engineering services, a builder sells his building services, I could go on all day. Comparing us to car salesmen is a stretch, but sometimes I also say things to make a point that may be an exaggeration, we all do. What exactly do you do for a living, and what experience you had in the past caused you to have such a hair across your you know what about ICF? If you refer to someone above as "your contractor" I thinks its safe to assume you are not a builder, so what career is it that makes you son enthralled with ORNL and DOE2 reports? Just curious, that's all... |
|
|
|
|
Dana1
 Senior Member
 Posts:6991
 |
29 Jan 2013 02:13 PM |
|
Posted By Lbear on 28 Jan 2013 09:08 PM
* EPS Steady State R-Value (thermal resistance of the material)…. R - 23 (R - 4.55 / inch @ 40 degrees Fahrenheit)
Again you throw out a performance number a temperature that is completely irrelevant to most of residents of the US. The ~R4.5/inch number is the performance when 40F is the AVERAGE TEMPERATURE THROUGH THE MATERIAL, not when the exterior is 40F. So, yeah, when it's +10F outside, +70F inside, that's about how well it performs in an ICF. If +10F your wintertime outdoor average, not daily low, but wintertime AVERAGE, great, use that number! But that only applies to the tiniest fraction of the US population (not even a majority of the population in Alaska!) If you live in the cooler parts of US climate zone 7 (International Falls MN, say) that will be a reasonable estimate of it's wintertime performance, but even on the warmer edge of zone 7, (such as Fargo ND, or Anchorage AK) the 10-coldest weeks binned hourly temp is warmer than that. For Zone 5 the wintertime average performance of your example ICF would already be under R22, and in warmer zones it would be lower still. Calling it R23 steady-state just because there happens to be a 40F rating on the spec sheet is pure BS, since that's not the average temperature through the EPS most readers of this forum are going to experience. Calling EPS R4.5/inch in an ICF for most of the US is as bogus as calling polyiso R6/inch in a cold-climate sheathing application. (In International Falls iso should be derated to ~R5.5/inch if it's only the exterior third of the insulation, if you want to estimate the real performance in the application.) Using R4.5/inch for EPS is reasonable in exterior sheathing applications when it is less than half the total R in climate zones 5 or 6, but not in ICFs. Since you don't really HAVE to make stuff up or exaggerate to demonstrate the relatively good performance of ICFs, it's better to stop using irrelevant datapoints when trying to make the case. |
|
|
|
|
Dana1
 Senior Member
 Posts:6991
 |
29 Jan 2013 03:14 PM |
|
Looking back at the original post for this thread sphingers writes, "By the way the home will be in Central Florida....HOT." Better derate that R23 to ~R20-R20.5 for him, since the average temp through the ICF will be north of 85F during the cooling season, not the R4.15- R4.2/inch it would be rated for an 70F or 75F average temp through the material. An ICF that fat has no economic or comfort advantage in his location- shopping around for a cheap R16 (yes, they still make 'em) would be about right as an ICF solution, or going poured concrete with 2-3" of rigid exterior EPS if the quotes are cheaper and the contractor has proven methods using that approach. (Furring through-screwed to the concrete works fine for securing the foam, whether interior or exterior, it's easy to hang just about any kind of siding or wallboard on the furring. For FL hurricane resistance exterior furring may need to more substantial than 1x pine though.) ICFs are great and all, but not always the best investment. Insulate the walls sure, but if other methods are cheaper spending the difference on a higher-R attic and/or better windows may be a better place to put his money. But when labor costs are high and with "time is money" factored in, the case for a minimalist ICF might still be made here. |
|
|
|
|
Lbear
 Veteran Member
 Posts:2740
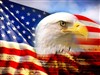
 |
29 Jan 2013 09:20 PM |
|
Posted By Dana1 on 29 Jan 2013 02:13 PM
Calling it R23 steady-state just because there happens to be a 40F rating on the spec sheet is pure BS, since that's not the average temperature through the EPS most readers of this forum are going to experience. Calling EPS R4.5/inch in an ICF for most of the US is as bogus as calling polyiso R6/inch in a cold-climate sheathing application. (In International Falls iso should be derated to ~R5.5/inch if it's only the exterior third of the insulation, if you want to estimate the real performance in the application.)
Using R4.5/inch for EPS is reasonable in exterior sheathing applications when it is less than half the total R in climate zones 5 or 6, but not in ICFs.
Since you don't really HAVE to make stuff up or exaggerate to demonstrate the relatively good performance of ICFs, it's better to stop using irrelevant datapoints when trying to make the case.
When you correct the R-Values of wood frame and cellulose or fiberglass do you use such language as you do for the above? I am just at a loss why you call the manufacturers data specs "BS" but I don't see you using that same language/emotion when it comes to data specs from wood frame building systems? My observation is echoed by others. I didn't make up anything or exaggerate anything. I simply copied the manufacturers energy specs and posted them on the forum. I didn't do the calcs, I didn't make them up. I have YET to personally find a stick frame builder that will detail a wood frame home to the point where it is significantly air tight. You know that leaking wall structures derate the R-Value of the insulation. Reading the posts here shows that I am not alone in this issue. When forum users were building their homes, many of those forum users had to go back and fix the detail work of their contractors. This is a luxury that many don't have, as they have families and jobs that would not allow them the time to fix those details while their home is being built. The point of this is that with ICF, it is by nature air tight. Of course windows and doors have to be done correctly but that also applies to wood frame. When it comes to a wall assembly, stacking ICF and pouring 6" of concrete within the core produces a very tight wall assembly. Doing the same with wood is not as easy because it requires greater detail that most contractors will not go to the extent of. In addition, wood frame builds involve many different trades and all it takes is one of those trades to drop the ball and you have a poor wall assembly. Are there wood framed homes that are tight? Yes, of course but they are either owner/builder or they paid a hefty price tag to find a contractor that does tight stick frame builds. So if you are going to be that critical of ICF then you should not be disingenuous and do the same for wood frame. If someone posts an R-Value of R-20 or whatever on a stick frame wall with cellulose or fiberglass, respond in the same fashion. Call it "pure BS" and factor in the thermal bridging of the studs, the lack of details of the framers, the insulation tech who didn't pack the wall as tight as he should with cellulose, the guy nailing the OSB who left a larger gap between sheets, the company that did the exterior house wrap, the fiberglass batt that was not put in correctly, etc. Then factor in the air leaking through the wall assembly and de-valuating the R-Value of the entire wall assembly. How many ICF projects have you done? Do you recommend ICF of are you mainly stick frame? |
|
|
|
|
Dana1
 Senior Member
 Posts:6991
 |
30 Jan 2013 06:43 PM |
|
Actually, I DO point out the performance differences of other insulation types & construction methods relative to as-installed or temperature variations quite regularly, including pointing out the difference between center-cavity vs. whole-wall R on stick frame (on nearly a daily basis on this website!) If the manufacturer's spec has a pinky on the scale squeaking out a 5-10% difference between true performance in most real world installations it's worth pointing out rather than parroting it like as if it were gospel. The 40F spec for EPS is not a valid spec in an ICF for most people for the reasons stated, whereas it IS a reasonable spec in an exterior sheathing app in a cold climate, but definitely NOT in a hot climate. ICF vendors who apply the 40F number to the whole assembly really ARE being disingenuous because over the ASTM C518 test range the wall would fall well short of that, and it doesn't take a building scientist to spot the error in reasoning. (If the average heating season temp of the concrete is 40F it's legit, but that will never be the case in US climate zones 1-6 or even for most of the population of Canada.) I call it BS here because it's intentionally being disingenuous- the manufacturers DO KNOW BETTER, and some have a history of even more egregious performance claims (worthy of FTC intervention.) I have similarly called the ASTM C518 ratings of low-density R23 and R19 batts BS (both here, and on other forums) because when installed in the very 2x6 cavities they are designed for, they are at a different thickness than their tested loft, and BY THE MANUFACTURERS OWN PUBLISHED DATA perform 5-10% lower than the ASTM rated value even at center-cavity. As with the EPS in an ICF, it's utter BS, because the labeled-marketed value is KNOWN not to be the as-installed performance for the majority of cases. They're only allowed to label an R23 batt as such because they're allowed to test at the manufactured (arbitrary) 6.25" loft, not the as-installed 5.5" nominal compressed thickness where it performs at about R20(!), according their own data. But even though it's BS for center-cavity R, a change from R23 to R20 doesn't move the whole-wall number very much. A true R23 at center cavity in a 25% framing fraction results in an R13.8 wall, assuming wood siding and gypsum interior. A true R20 center cavity studwall comes in at R13.1. It's only about a 5% difference, (just like calling an ICF that really performs at R21-R22 in most installations an R23 wall :-) ), but it's BS just the same, and should be labeled more appropriately. I've often point out that fiberglass batts above a certain density and cellulose both increase performance slightly as temperatures drop, particularly in wall assemblies, but only if they're installed nearly perfectly. I also regularly point out that low density fiberglass in horizontal assemblies without topside air barriers fall woefully short of their ASTM C518 rated performance when at the temperature extremes, whereas cellulose and high-density (1.8lbs/cubic-foot or better) fiberglass DOES hold up. The tightness of cellulose has very little effect on it's center-cavity R value- in fact over 2.8lbs density it's R-performance begins to fall a bit. With the thermal bridging of the framing it takes a rather LARGE change in the center cavity R to move the whole-wall R up or down by even 5%. (As I point out to folks thinking about filling the cavity with closed cell foam, my motto is "I it's the thermal bridging, stupid- save the foam budget for the exterior!") I've never done a whole house as ICF. I've recommended ICFs for whole houses, but more often for foundations, particularly in high labor-cost locations, or on time-critical projects. I was personally involved in a deep energy retrofit on a 3 story balloon framed house with a full basement that came in at 464cfm/50 in the past year, a tightness <1ACH/50, and a tightness hit far more easily in new construction with 4x8 sheet sheathing than this plank-sheathed antique beast of a house. And there are performance builders who can hit that every time. Canadian R2000 builders hit it (nearly) every day, even thought the spec allows 1.5ACH/50. Under IRC 2012 all homes would have to be under 3ACH/50, but that's been proven remarkably easy to hit, even with stick built. It's pretty easy to make ICF homes that tight, but most aren't unless they're actually trying (or required to by local code.) It's not rocket science- it's goop science, and even ICF builders would need to get with a more rigorous air tightness program to hit under 1ACH/50 every time. Just because it's comparatively easier to make an ICF or SIP air tight doesn't mean they are inherently air-tight. Any time you think something is foolproof a more creative fool will prove you're wrong. But even code-min 3ACH/50 tightness is a pretty reasonable number for an R20 whole-wall house from an energy use perspective, and spending a lot of money making it half-that or a third that may not always be the best investment. Of course you can point out that tract housing production builders still build crap (and they do) but anybody spending the kind of money it takes to build an ICF house isn't in that market. And anybody looking for price/performance can usually find stick-framed builders that "get it", as well as ICF & SIP builders who regrettably, don't. |
|
|
|
|
Lbear
 Veteran Member
 Posts:2740
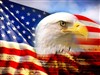
 |
30 Jan 2013 09:13 PM |
|
Posted By Dana1 on 30 Jan 2013 06:43 PM
It's pretty easy to make ICF homes that tight, but most aren't unless they're actually trying (or required to by local code.) It's not rocket science- it's goop science, and even ICF builders would need to get with a more rigorous air tightness program to hit under 1ACH/50 every time. Just because it's comparatively easier to make an ICF or SIP air tight doesn't mean they are inherently air-tight. Any time you think something is foolproof a more creative fool will prove you're wrong. But even code-min 3ACH/50 tightness is a pretty reasonable number for an R20 whole-wall house from an energy use perspective, and spending a lot of money making it half-that or a third that may not always be the best investment. Of course you can point out that tract housing production builders still build crap (and they do) but anybody spending the kind of money it takes to build an ICF house isn't in that market. And anybody looking for price/performance can usually find stick-framed builders that "get it", as well as ICF & SIP builders who regrettably, don't.
You are stating that "most" ICF homes "aren't" tight. Can you provide some data to show that? When building stick frame homes, most contractors do not build tight homes. Finding a builder that will build a tight stick frame home is not easy and comes at a premium price. The other option is to pay a consultant to work on the project with the contractor and the consultant oversees the build and the different trades involved in order to get the home built correctly. So when it comes to price/performance, the numbers are not always clearly represented with stick frame builds. They don't include all the fees and surcharges for getting that home up to snuff.
Posted By Dana1 on 30 Jan 2013 06:43 PM
I've never done a whole house as ICF. I've recommended ICFs for
whole houses, but more often for foundations, particularly in high
labor-cost locations, or on time-critical projects. Thank you for your honesty. I assume you have at least been INSIDE of an ICF home, am I correct?
Posted By Dana1 on 30 Jan 2013 06:43 PM
Actually, I DO point out the performance differences of other insulation
types & construction methods relative to as-installed or
temperature variations quite regularly, including pointing out the
difference between center-cavity vs. whole-wall R on stick frame (on
nearly a daily basis on this website!)
Can you
find me a post where you come out and state, "pure BS" against stick
frame R-Value claims? I don't remember you using that terminology except
for ICF.
Posted By Dana1 on 30 Jan 2013 06:43 PM
But even though it's BS for center-cavity R, a change from R23 to R20
doesn't move the whole-wall number very much. A true R23 at center
cavity in a 25% framing fraction results in an R13.8 wall, assuming
wood siding and gypsum interior. A true R20 center cavity studwall comes
in at R13.1. It's only about a 5% difference, (just like calling an
ICF that really performs at R21-R22 in most installations an R23 wall
:-) ), but it's BS just the same, and should be labeled more
appropriately.
Let me understand this correctly.
You stated above that because ICF claims R-23 when it's really
R21-R22, it's on the same category as when wood frame claims of R20 is
really R13. |
|
|
|
|
dmaceld
 Veteran Member
 Posts:1465
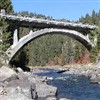
 |
30 Jan 2013 11:34 PM |
|
My brother was in the manufactured home business for several years, leaving it about 8 years ago. Even back 10 to 15 years ago manufactured houses were being built good and tight. Walls are usually 6" packed w/ cellulose insulation. Every joint is caulked so air leakage into the house is extremely low. We were talking about house construction methods and he commented that the one thing the buyers of the newer and better built manufactured homes never complained about were their heating bills!
|
|
Even a retired engineer can build a house successfully w/ GBT help! |
|
|
Dana1
 Senior Member
 Posts:6991
 |
31 Jan 2013 11:57 AM |
|
"You are stating that "most" ICF homes "aren't" tight. Can you provide some data to show that?" I've previously posted an air tightness studies comparing homes in TX where in the ICFs sampled the ACH/50 average was in the 5-ish range: http://eec.ucdavis.edu/ACEEE/2002/pdfs/panel01/04_289.pdf Avoiding stupid-attacks like recess lights on the top floor probably would have made the difference, but that's pure speculation on my part, since the locations of the leakage wasn't detailed. The data are out there, but it's in drips & drabs. If you're in show-me mode, I invite you to show me an industry report that gives a different air tightness number over a reasonable sample indicating that the homes in the TX study were outliers. BTW: A vendor of sheet EPS was selling it labeled at the 40F test numbers rather than the 75F ASTM C518 number it would be in violation of FTC regs. Because ICFs are not purely insulation they get away with using the 40F test numbers by putting in a spec rather than a label, but it's clearly intended to deceive. I'd hazard that nine out of ten BUILDERS & ARCHiTECTS who read that spec assume that it refers to a 40F outdoor temp rather than the average temp through the the material, and a much higher fraction of home buyers would too. Most people designing and simulating for specific performance goals in a particular climate/site would not make that assumption. " I assume you have at least been INSIDE of an ICF home, am I correct?" Yes, I have been inside an all-ICF home (more than one), and a portion of my own home is built with ICF. While the local ICF homes I've been in are better than code-min, they're NOTHING like the true high-performance deep energy retrofit I helped my friend with on his 3 story balloon framed house a few miles away. (~R40ish wholewall, ~R60-ish roof, U0.18-0.20 windows throughout, <1ACH/50.) But to assume that I'm down on ICF would be a mistake, even as I criticize the marketing sleight of hand. As stated previously in this thread there is no NEED to make these types of exaggerations, given the pretty good true performance of ICF. "Can you find me a post where you come out and state, "pure BS" against stick frame R-Value claims?" Search functions aren't very good on this site. I may have used the more legal term "fraud" rather than BS most recently, but I assure you I've used similar terms regarding ASTM C518 lableling on batt insulation. See response 17 & 28 on this thread (another forum). I've made similar comments on this website, some less polite than stated on that thread. http://www.greenbuildingadvisor.com/community/forum/general-questions/25395/why-there-such-bias-against-fiberglass Curiously and R21 high density batts perform at R21 in a 2x6 cavity, whereas an R22s & R23s only hit R19-R20. The low density R22s & R23s are cheaper than the R21s, but the labeled R is still higher, making them APPEAR like the better deal. Compare the R22s vs R21 performance in a 2x6 cavity in the Owens Corning compression chart: http://www.owenscorning.com/literature/pdfs/10017857%20Building%20Insul%20Compressed%20R-Value%20Chart%20Tech%20Bulletin.pdf Other manufacturers have similar charts, but not all are online. How is that not utter BS or even fraud? It's in the minutae of the wording of the labeling regulations. "Let me understand this correctly. You stated above that because ICF claims R-23 when it's really R21-R22, it's on the same category as when wood frame claims of R20 is really R13. " Nobody in the code or building science biz has ever considered the center cavity R of a stick-framed house as equivalent to continuous insulation methods, and it's not fraud or BS to use the enter-cavity R at the installed loft to represent the R value of the insulation fraction of the wall. But the whole-wall performance requirement enshrined in code-minimums are pretty equivalent between cavity-insulated and continuous-insulated assemblies. (Eg: R20 cavity 2x6 is pretty equivalent to R13 2x4 + 5 continuous insulation, etc.) Only ignorant or unsophisticated builders & architects would be confused by that, but it's probably a common misconception/lack of understanding amongst home-buyers of typical low-to-middlin' performance homes, less so for those looking for high performance. An R20-ish wall is a pretty good wall- better than code even in climate zones 6-8. But it's not a particularly high performance wall in zones 5+. It's nearly impossible to get to Net Zero with anything under R30 even in zone 5, or under R40 in zone 6, with corresponding upgrades to other assemblies. The greenbuildingadvisor "pretty good house" concept for zone 6 is U0.20 /R5 windows, R10 sub-slab, R20 foundation wall, R40-whole-wall for above grade, and R60 roof/attic, and most of those COULD become net-zero with photovoltaic panel arrays that actually fit on the roof. Wall-R is just part of the equation, but it's an important part, and it's pretty expensive and makes for a fairly thick wall to hit a true R40 with ICF. My friend's DER hit pretty close to R40 with cellulose cavity fill on a full-dimension low framing fraction 2x4 wall and 4.5" exterior polyiso at about 11" from paint to paint. An R40+ ICF would be well over a foot even without siding & interior gypsum, which is but one reason I shy away from them for high-performance homes in my climate zone. But in climate zones 3 & 4 ICF can be a pretty good option even for Net Zero designs. In climate zone 1 & 2 maybe, but there may be more cost-effective ways to get there. The original poster wasn't looking for anything like Net Zero, but an R20-R22 ICF could get you there in a central FL climate, provided the rest of the design was up to snuff. The prescriptive code min under IRC 2012 for mass walls with at least half the R on the exterior for zone 2/central FL is a measly R4, and even the worlds cheapest R16 ICF is 400% of code. I wasn't kidding when I recommended seeing if 2-3" of exterior EPS was cheaper and spending the money elsewhere, since 3" of exterior EPS would already be 3x code min, and the bulk of the heat gain is from other factors like roofs & windows, with walls being a distant third. While ICF construction would be really nice there, it wouldn't be a performance driver, and if it's more expensive than poured concrete with R8-R12 exterior rigid EPS, upgrading to ICF is not necessarily going to be a value proposition for him. |
|
|
|
|
Lbear
 Veteran Member
 Posts:2740
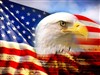
 |
31 Jan 2013 01:36 PM |
|
Posted By Dana1 on 31 Jan 2013 11:57 AM
Yes, I have been inside an all-ICF home (more than one), and a
portion of my own home is built with ICF. While the local ICF homes
I've been in are better than code-min, they're NOTHING like the true
high-performance deep energy retrofit I helped my friend with on his 3
story balloon framed house a few miles away. (~R40ish wholewall,
~R60-ish roof, U0.18-0.20 windows throughout, <1ACH/50.) But to
assume that I'm down on ICF would be a mistake, even as I criticize the
marketing sleight of hand. As stated previously in this thread there is
no NEED to make these types of exaggerations, given the pretty good
true performance of ICF.
As you said yourself,
the law of diminishing returns. What are the true market costs to do
such a retrofit and what is the ROI? It's a lot different when someone
has to pay consultation fees, labor and construction costs vs. having a
buddy do it for them. You are also aware that ICF manufacturers
have forms that have thicker exterior facing foam or they allow one to
add foam panels to increase the R-Value up to R-40 for use in Zones 6 or
higher. We are comparing wall structures so roof values and window
values are inconsequential.
Posted By Dana1 on 31 Jan 2013 11:57 AM
"You are stating that "most" ICF homes "aren't" tight. Can you provide some data to show that?"
I've previously posted an air tightness studies comparing homes in TX
where in the ICFs sampled the ACH/50 average was in the 5-ish range: http://eec.ucdavis.edu/ACEEE/2002/pdfs/panel01/04_289.pdf
Avoiding stupid-attacks like recess lights on the top floor probably
would have made the difference, but that's pure speculation on my part,
since the locations of the leakage wasn't detailed. The data are out
there, but it's in drips & drabs. If you're in show-me mode, I
invite you to show me an industry report that gives a different air
tightness number over a reasonable sample indicating that the homes in
the TX study were outliers.
According to the study you referenced, they did state the location of the air leakage: "in
one case the ICF home was tighter than the frame home while in the
other the trend was reversed. This may be attributed to the fact that
only the walls of the ICF homes were constructed differently from the
frame structures, while the slab-on-grade foundation and wood-framed
roof designs were similar. Construction details at the attic and at the
junction of the first and second floors are critical to the airtightness
of these homes, as is the amount of duct leakage."So
basically the roofs leaked like crazy and the details in
the stick frame attic were atrocious as were the details in the floor
junctions. This was noted in how the stick frame homes leaked air just
as bad, as they were 5.0 & 5.1. They might as well should have left a
window open or just left a gaping hole in the wall when they did the
blower door test. You picked out a very poorly done study
and even so it showed that stick frame homes leak air just as bad when
the roof details were poorly done. One did not need a study to tell us
that. Even so, the ICF walls still performed better. Your example study proved nothing other then a leaky roof will give you a leaky home and whether you build the walls out of wood or concrete, a leaky roof gives you a leaky home.
Posted By Dana1 on 31 Jan 2013 11:57 AM
If you're in show-me mode, I invite you to show me an industry report
that gives a different air tightness number over a reasonable sample
indicating that the homes in the TX study were outliers. ICF Blower Door StudyStudy There are plenty of studies that prove that ICF walls are much more air tight than stick frame walls. If you compare wall structure to wall structure, the answer is clear. If you take your example study which clearly admitted that the roof was very leaky, you get an unclear answer. Posted By Dana1 on 31 Jan 2013 11:57 AM
Nobody in the code or building science biz has ever considered the
center cavity R of a stick-framed house as equivalent to continuous
insulation methods, and it's not fraud or BS to use the enter-cavity R
at the installed loft to represent the R value of the insulation
fraction of the wall.
That sounds contradicting to me.
As Bill O'Reilly states, "I am a simple man" and what you stated above
is a contradiction. In one instance nobody considers center cavity
insulation R-Value of a stick frame home to be equivalent or
representative of the true R wall value but then it's OK to use the
center cavity R value to represent the insulation value of the wall, yet
it's not a true number. So it's OK to give a false representation of a stick framed wall R value because everyone knows it's false. |
|
|
|
|
toddm
 Veteran Member
 Posts:1151
 |
31 Jan 2013 04:09 PM |
|
Give it a rest Lbear or whoever you are. The MIT study was bought and paid for by the concrete industry. If memory serves, TexasICF averred in a post that he had nominated some of his finest work as candidates for the study. For Texasicf, Brian and the other sales types here, people come here to OVERCOME sales pitches, to get a handle on the answer before they ask the question. If your goal is to turn them off on ICF you are doing a bang-up job. |
|
|
|
|
ICFBdr
 Basic Member
 Posts:232
 |
31 Jan 2013 04:53 PM |
|
Just because the Concrete Industry Sponsors the testing, does not mean they paid for positive results. I highly doubt MIT would risk their reputation for a couple bucks. It would make more sense to me that the Concrete Industry's faith in the product gave them the confindence to spend the money prior to the testing. In other words - they knew it would reflect well on them before the researchers even began the study. It seems that anytime a study/test shows anything positive for ICF it is automatically viewed as "marketing hype" or "salesman BS." Has anyone considered the possibility that this is simply a way to build an energy efficient home that is inherently air tight and easy to heat/cool? I have seen some over-the-top claims from some manufacturers' websites, but that does not automatically mean everytime a claim about the efficiency of ICF is made that it is "bought and paid for" by the Concrete Industry/ICF manufacturer. |
|
|
|
|
Dana1
 Senior Member
 Posts:6991
 |
31 Jan 2013 05:22 PM |
|
Lbear: Yes, I undestand that it's possible to hit R40+ with some ICF systems. But it's not usually the most cost effective way to achieve the thermal performance, and it's a pretty fat wall. The financial aspects of high-R buildings is partly in reduced (or eliminated) mechanical equipment costs, and it's not 25 years to NPV+ if natural gas is the heating fuel, but it can be if heating oil is the only option. The Building Science folks took a stab at where the easier-to-analyze R-value limits are, broken down by climate zone, but with the caveat that local material/labor costs and local energy cost can skew their middle-of-road recommendations by quite a bit. IRC 2012 code min is still a 25 year payback in some locations, but sub-10 in others. The BSC middle-of-road takes a longer lifecycle view, and the recommendations can be found in Table 2, p10 of this document: http://www.buildingscience.com/documents/reports/rr-1005-building-america-high-r-value-high-performance-residential-buildings-all-climate-zones Note that in their table R40 wall R doesn't show up until zone 7, but in high-energy cost markets in zones 5 & 6 there can still be a rationale, especially when using a lowest-cost (="not ICF") approach. The link labeled "ICF Blower Door Study" doesn't mention blower doors or offer any air tightness data. It does offer a big "ICFs are more efficent than current code min stick built" kind of shocker conclusions (as if anyone would be surprised by that?!) The link labeled "Study" didn't give data on the sample of 15, the one example given hit 2.23ACH/50 (Congratulations, it even meets code!), and is about 3x as leaky by all measures including ACH/50 as by friend's DER on a balloon framed plank sheathed antique. The text cited in the referenced TX study didn't really speak to the specifics, only hinted at it. It basically says that the builders didn't even try to make them air tight. (The duct leakage issue makes them perform even worse than a tight-ducted house.) So what if the stick built sub code crap in the same study performed no better or even slightly worse than the ICFs? I was never asserting that stick built was inherently tighter, only that the presumed air-tightness of ICF can't be presumed, and damned few were as tight as my friend's <1ACH/50 retrofit. In that particular small study NONE of them would meet IRC 2012 code for air tightness, yet 10s of thousands of stick built units out there do. And the vast majority of the tens of thousands of R2000 homes built since 1980 are stick built, and tested <1.5ACH/50 as part of commissioning. (I'm not sure what fraction tested <1ACH/50, but it's not rare.) But I'd bet that as a retrofit it would be easier to pull the ICF houses in that TX study into compliance. But that doesn't mean stick-builders with even hint of goop-science can't make an OSB or plywood sheathed building as air tight as any ICF without much expense- it's only a matter of training the crews to get them into the habit- the extra labor is negligible. Under 1.5ACH/50 is tougher, but in a building with mere R20 whole-walls it's a "who cares" kind of difference between 3ACH and 1.5ACH. (Air leakage issues become a bigger fraction of the total heat loss/gain at higher R values.) Since you're still in show-me mode, show me the "plenty of studies" that demonstrate how much tighter ICF is than stick built, ones with real numbers, eh? (Really- I'd like to see something other than onsie-twosie studies or "representative examples" of a larger study!) So far you've shown me exactly one study with the numbers for exactly one house. (I at least dug up four, two crappy stick-built and two crappy ICFs. :-) ) C'mon, if they're plentiful, they should be easy to find! While I firmly believe it's easier to make an ICF tight, experience shows that it's also not hard to make a stick built house air tight when code or builders/buyers demand it. Now that there's a 3ACH/50 hurdle to clear the former crummy tract building crews are having to come up to speed on that, and some ICF builders will need to step up too. If you're using Bill O'Reilly as your authoritative source on ANYTHING I'm going to have to admit defeat and slink away! It's not false to state what the center cavity R is, (even if the batt vendors play games with that for labeling purposes- use the compressed-batt data in lieu of label), nor is it false to use center-cavity R to characterize the thermal performance of a stick framed wall, which falls within a reasonably tight range over the typical range of framing fractions. A 2x6 fiber or open cell cavity filled wall is nearly always going to run between R13 and R15 for whole-wall R, (concentrated toward the R13 end in the real world) independent of stud spacing and other typical framing differences. It takes quite a large framing fraction to bump it to R12. But it IS false to say that continuous insulation R is the same as center-cavity R, and I doubt anybody who has thought about it for more than 7 minutes wouldn't understand it. Running the U-factors on framing fraction for a 2-D model does NOT take hard math. Code drafting bodies and designers/architects have long understood the difference, even if it's still a bit fuzzy to simple guys like Bill. The cavity insulation can only insulate the fraction of the wall that it actually covers, it's not a hard concept. But it does reasonably represent performance at typical framing fractions. When the majority of the housing stock is being built that way, using center-cavity R is a reasonable shorthand for comparative purposes between other stick-built structures. I didn't invent it, and I'm not crazy about it (I'd prefer more precise whole-wall Rs), but I understand how it got to be that way. Hint: It wasn't a fraud or a finger on the scale perpetrated by fiber insulation manufacturers (even though they're far from immune to exaggerated claims.) OK, invoking his holy highness O'Reilly was the last straw- I'm done here! :-) But if you're able dig up the statsitical studies of ICF air tightness with real blower door test ranges & averages, DO start a new thread on that subject, eh?
|
|
|
|
|
toddm
 Veteran Member
 Posts:1151
 |
31 Jan 2013 07:06 PM |
|
TexasICF on June 12, 2011: (snip): I do appreciate your opinion and the link to the report from a few posts back. I contributed 15 Texas houses to the recent MIT study. MIT reported ICF buildings to be 20% more efficient than conventional. I believe this 20% better number is low (at least for Texas). (anip) http://greenbuildingtalk.com/Forums/tabid/53/aff/4/aft/78798/afv/topic/afpg/3/Default.aspx BTW, the 20 percent figure compares ICF to code min stud walls (less R value) not clear if IRC06 or 09. |
|
|
|
|
Lbear
 Veteran Member
 Posts:2740
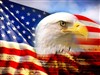
 |
31 Jan 2013 08:20 PM |
|
Why do these discussions devolve to personal attacks and conspiracy theories? Of which ToddM is at the forefront of these attacks. The term "internet bully" comes to mind.
By the way, my referencing Bill Oreilly had to do with his statement of , "I am a simple man" and it had nothing to do with him as an authoritative source. It's basically the premise that people complicate matters that are not that complicated, just to cause a diversion to avoid addressing the issue. I assume by your statement that you dislike the man but the fact is that he is one of the last hard hitting journalists out there and he doesn't drink the KoolAid of the right or the left. I now know what side you lean towards but that is another topic altogether.
|
|
|
|
|
arkie6
 Veteran Member
 Posts:1453
 |
01 Feb 2013 12:41 PM |
|
Posted By BrianBaron on 29 Jan 2013 01:50 PM
...If you are still referring to old statement that was made about the "Effective R-Value of 50+" from the R-22 form... I agree that was a bit of BS, ...
It is not really BS if you look at how the information is used. When looking at wood framed construction, almost everyone, at least until the last few years, referred to the wall's insulating value as whatever the R value was of the material stuffed in the cavity between the studs and plates. If you had a 2x4 wall with R13 fiberglass batts between the studs, that was an "R13 wall". In reality, when you factor in the higher thermal conductivity of the wood framing, the actually wall R value was approximately 9-10. Similarly with a 2x6 wall @16" OC with R19 batts was an "R19 wall" when in reality it only comes in at around R14-15 accounting for the wood framing. And most if not all of the heat load calculating programs of a few years ago just used the cavity insulation value as the input for the wall R value, i.e. "R13" was the value input for a 2x4 framed wall with R13 fiberglass batts. Now lets assume we try to make a wood framed wall with comparable insulation value to an ICF wall rated R22 which is pretty close to actual due to virtual elimination of the thermal short circuits. How much R value would you have to stuff in the wood framing cavities to equal R22 whole wall? A lot more than you think. Somewhere around R45. As an example, say we build an imaginary 7" thick wood framed wall with studs @ 16" OC and fill it with closed cell spray foam at R6.5/inch. The cavity R value would be 7" x R6.5/in = ~R45. The whole wall R value for this assembly is ~R22 assuming R1.25 per inch for wood framing and a 25% framing fraction. When calculating your heat losses, your HVAC contractor would input R45 for your heat loss calculation when in fact, the total wall R value is actually closer to the R22 of the ICF wall. |
|
|
|
|
BrianBaron
 New Member
 Posts:76
 |
01 Feb 2013 01:16 PM |
|
Arkie, I am the last person that is going to argue against the effectiveness of ICF vs Stick Built, or any other method for that matter. I was implying that in the sales process, most did not explain the details of that comparison to a customer. If explained correctly, it can be a good analogy... If you just tell someone that a R-22 ICF wall is the same as a R-50 stick built wall, then its a bit untrue. |
|
|
|
|
Dana1
 Senior Member
 Posts:6991
 |
01 Feb 2013 03:33 PM |
|
Posted By BrianBaron on 01 Feb 2013 01:16 PM
Arkie, I am the last person that is going to argue against the effectiveness of ICF vs Stick Built, or any other method for that matter. I was implying that in the sales process, most did not explain the details of that comparison to a customer. If explained correctly, it can be a good analogy... If you just tell someone that a R-22 ICF wall is the same as a R-50 stick built wall, then its a bit untrue.
From purely an energy use point of view the better analogy would be to compare it to standard 2x6 stick built with 2" of exterior foam- bump that to 2.5" if EPS rather than iso or XPS. To get to a rationale for calling it R50 would have so many caveats about where/when/how/what conditions that even my lawyer couldn't read it.  From a quietness in the wind and structural capacity point of view there's no comparison- ICF wins by several furlongs. I was pushing the merits of ICF to my in-laws several years back when they built on the top of windswept hill with nice New England foliage views, but after the initial sticker shock on competing ICF quotes they opted for 2x6 + R7.5, spending the difference on radiant floors and nicer interior finish. I'm not sure if they regret it, but I often notice the sound of the wind when visiting their (VERY nice and quite comfortable) house- it's not a screamer, but I'm confident ICF would have been quieter. They've since had to adjust the venting on the wood-burning stoves to avoid backdrafts from wind currents too. It's better than code, but not what I'd call a high performance building for their cool edge of climate zone 5 location. (At current heating oil prices the financial rationale for going much higher performance is clearly there, but in 2005 who knew?) |
|
|
|
|
toddm
 Veteran Member
 Posts:1151
 |
01 Feb 2013 03:49 PM |
|
There are two problems with this comparison. The first, which continues to this day, is its assumption that home buyers can't get the foam without the concrete. In fact, no one would spend a minute thinking about how to pack R-45 between the studs. They'd switch to foam sheathing even if they knew nothing about whole-wall R values vs stud bay r values, and in doing so, the ICF advantage would begin to disappear. This misdirection is particularly egregious here. No one who wants a code min stud wall winds up reading GBT. The second problem is the comparison's use of a commercial buildiing code compliance model to develop thermal mass numbers which the authoring engineering firm itself acknowledged was not appropriate for this use, (although probably good enough to compare A with B.) Once again, we're back to the mystery of why DOE2, which was develoiped specifically for this purpose, is being studiously avoided by ICF industry. No, Brian, I'm not asking you to pony up ~$80k or so necessary to make a legitimate thermal mass claim. I am saying that if you are not willing to meet the FTC's requirements for a standard test, then shut up about thermal mass. And kudos to Dana1 for pointing out that the FTC polices labels as opposed to specification sheets. |
|
|
|
|
Dana1
 Senior Member
 Posts:6991
 |
01 Feb 2013 06:01 PM |
|
ICFs don't NEED no steekin' ASTM C518 tested label, since it's not being marketed as strictly insulation product, but as a wall system. SIPs don't either, and the under-rating of the thermal bridging of SIPs is also sometimes a marketing sleight of hand, but I've yet to see a SIP vendor use the 40F test value for EPS rather than the 75F number as seems all to common with ICF vendors. I've seen some pretty aggressive statements about the R-values of polyurethane core SIPs though, which appear to be using initial R rather than aged R, and ignoring all of the thermal bridging at the plates, window framing, etc. (Yeah, right this SIP performs at R7/inch, straight across... and all the knobs on my guitar amp go to 11 too , not the usual 10, see, 11, 11, 11, 11...) EPS rigid sheet product and products like batts DO need that label, since it's being sold as insulation to be incorporated into assemblies, not a system, the theory being that it's then possible to do apples-to-apples performance comparisons. That theory kinda-works, but then kinda-doesn't sometimes, as in the tested vs installed loft of low density batts. But the performance of the assembly into which it gets installed is entirely up to the designer/installer. It doesn't take an idiot of Bill O'Reilly's creativity to figure out how cut the legs out from under the labeled performance in a real world assembly. There are plenty of instances of people asking about spraying 5" of closed cell foam into 2x6 studwall cavites on this website, as foolish as that may sound. That 5" x R6= R30 really sounds great, but spending $5 per square foot just for the insulation portion on something that performs around R14-R15, not so much, when an inch of iso on the exterior of a cellulose or batt filled studwall delivers R19 or better. "It's the thermal bridging, stupid!" has yet to sink into the public consciousness, but it's the mantra of performance builders modeling real designs everywhere. The mass effect of ICF is real and models well with DOE2, but concrete is a fairly expensive thermal mass in $/MMBTU of buffering capacity, just as all-EPS insulation isn't exactly a $/performance leader for insulation. The real value proposition is in the structural capacity of building with concrete, but that's no always a choice-driver. Cheapskate high-mass low-energy home builders like Brian Carsten manage do do a lot with dumpster-dived-EPS scrap, stress-skins, and tons & tons of dirt- not exactly an approach that appeals to everyone ( including me), but you CAN get there from here at well under ICF cost. The mass effects of ICF is an overhyped value, value way behind structural aspects of building with concrete in my mind. (YMMV) As a system it's a quick & reliable way to insulate a concrete wall (or foundation assembly) to a decent value. But if you don't need/want/value the structural aspects, it's an expensive way to build from strictly a price/thermal-performance point of view, and that's why I don't expect it to displace timber framed wall assembles in US homes any time soon. While can still be cost-competitive for insulating foundations in high-labor cost markets (including mine), even there many performance builders still use sheet goods or spray foam, even at R15-R20ish values. I personally prefer ICF to other foundation insulation methods, for the simplicity of aligning foam sheathing of a timber-frame with the exterior EPS of the ICF to get a continuous thermal break that's comparatively easy to air seal- following the "It's the thermal bridging, stupid" line of thinking. It's pretty easy to park an ~R25-R30 whole-wall 2x4 foam sheathed assembly cleanly on top of a minimal R16-R20 ICF with excellent thermal breaks and good air tightness, which comes in at about 2x code min in my area, and it doesn't break the budget. Again YMMV. |
|
|
|
|
dmaceld
 Veteran Member
 Posts:1465
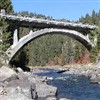
 |
02 Feb 2013 01:30 AM |
|
Posted By toddm on 01 Feb 2013 03:49 PM
Once again, we're back to the mystery of why DOE2, which was develoiped specifically for this purpose, is being studiously avoided by ICF industry. Maybe because it doesn't work that well for ICF? I've never used DOE2, or even looked closely at it, so I'm really not sure how to interpret what the ORNL authors wrote in their mass study report. Here's a quote from the Introduction. "Application of
the newly developed equivalent wall theory enabled whole building
dynamic energy analysis for complex three-dimensional wall material
configurations. Normally, complex building envelope components cannot be
accurately analyzed using one-dimensional computer models like DOE-2.
Typically, thermal modelers have to use simplified one-dimensional
descriptions of complex walls. This significantly reduces the computer
modeling accuracy because of the complicated 2 and 3-dimensional heat
transfer which can be observed in most wall assemblies.
In this work, response factors, heat capacity, and R-value were
computed for complex walls using finite difference computer modeling.
They enabled a calculation of the wall thermal structure factors and
estimation of the simplified one-dimensional equivalent wall
configuration. Thermal structure factors reflect the thermal mass heat
storage characteristics of the wall assembly. The equivalent wall has a
simple multilayer structure and the same thermal properties as the
complex wall. The equivalent wall and complex wall dynamic thermal
behaviors are identical. The thermal and physical properties describing
the equivalent wall can be used, very simply, in whole building energy
simulation programs with hourly time steps. These whole building
simulation programs require simple one-dimensional descriptions of the
building envelope components. In this work, DOE-2.1E was used to
calculate heating and cooling loads for six U.S. climates." What that says to me is the heat transfer characteristics of an ICF wall is more complicated than what DOE2 is designed to handle. They had to use a much more sophisticated program to develop an equivalent simple wall that would work in DOE2.
The report is here: http://www.ornl.gov/sci/roofs+walls/research/detailed_papers/dyn_perf/ |
|
Even a retired engineer can build a house successfully w/ GBT help! |
|
|
You are not authorized to post a reply. |
|
Active Forums 4.1
 |
Membership: |
 |
Latest:
dliese |
 |
New Today:
0 |
 |
New Yesterday:
1 |
 |
Overall:
34724 |
 |
People Online: |
 |
Visitors:
115 |
 |
Members:
0 |
 |
Total:
115 |
|
|
|